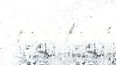
UPSTREAM INJECTION
I've tested upstream injection extensively on a few cars, all with different setups. The most extreme was my own, with fully 50% of my fuel being injected pre-compressor. Another good test bed was a heavily instrumented MR2 with a small sidemount IC and pre-compressor WM injection (just under 500 whp on pump gas). Here are a few key points, many of which never seem to get talked about on the internets.
​
-
Only that cooling which happens before Intake Valve Close increases airflow. Seems obvious, but it's worth mentioning.
-
Any injected liquid that doesn't vaporize before IVC will still provide cooling during compression, so all is not lost. Mostly, this helps lower knock risk and EGT. Pumping work is lower and some other obscure benefits that probably don't add up to anything apreciable.
-
Air density will vary at the same rate as the ratios of absolute temperatures. 10% drop in absolute temp is a 10% gain in mass airflow. To convert degrees F to absolute temp in degrees R, simply add 460 and take a ratio fo those temps. If you drop your charge temps from 150 degrees to 120 degrees, you can expect a 5% gain in airflow at the same boost.
-
Spraying pre compressor will assure excellent atomization and homogenization. On my own car I sprayed fully 50% of my total fuel pre turbo(s) and had no distribution issues as seen on individual cylinder O2 sensors (compound turbo 4 cylinder). I was spraying enough that it definitely was not all evaporating, so there was still liquid fuel in the air. Nothing mixes air and fuel like a compressor wheel spinning at 100,000 rpm.
-
"Time spent" in the charge air really isn't a factor in evaporation, there's just too little time to matter even if you double it. You can do some math to determine air speed in the charge piping, and then considering the length of piping, determine how much time there is. It's not much. There's a lot of talk about turbulence etc helping with this, but in my experience, there isn't enough basic evaporation happening to actually matter.
-
It seems to be nearly impossible to cool below the local boiling point (pressure corrected) of the fluid being injected. I saw great correlation on this at all boost pressures between 35 psi and 60 psi. Boiling will vaporize the liquid instantly, any further evaporation beyond that takes time, and there isn't enough time to matter in the charge piping.
-
Up to that boiling point temperature methanol injection gives very close to exactly as much cooling as the math predicts. Usually I'm within a few percent.
-
It's very difficult to measure the temperature of a wet mixture (air and methanol/water) where the two are at different temperatures. The liquid is thousands of times better at registering on the temp sensor than the air is, due to it's much higher thermal conductivity and density, and it can cling to the sensor. I believe that more often that not, someone's amazingly low intake temps near ambient are really just the sensor reading the temperature of the liquid (stored near ambient temp in the car) and mostly ignoring the air. Be careful what you believe from that IAT sensor. As is always the case with temperature sensors, you're always reading the temperature of the sensor itself, not necessarily what it's exposed to.
-
If un-vaporized fuel is thoroughly atomized and mixed with the air, the mixture will reach one temperature and read properly on the IAT sensor. Very little cooling is done here. Without the phase change, it's limited to the specific heat of the liquid, which is much much lower than its latent heat of vaporization. A good way to assure good atomization and mixing is to spray pre-compressor. This provides enough turbulence and exposed surface area of the whole mixture to allow heat to move from the air to the liquid.
-
My car made the same airflow at 85 psi non-intercooled as 60 psi air-air intercooled and 53 psi ice water intercooled. In all cases the dyno numbers support the airflow readings. Boost is just a byproduct of everything else. :o)  
I was not out to prove this point when I ran this setup on the car, in fact I hadn't even considered it as a possibility. I expected to achieve the predicted cooling for the amount of methanol injected. Only in looking at the data as it came in and in hindsight did this trend appear.
​
Personally, I'd prefer even a bad intercooler just to take the edge off the temps, as long as pressure drop is low. Coincidentally, many IC cores that don't cool well also have low pressure drops, it just needs to be big enough for your particular flow rate. In my experience poor air-air ICs still cool better than huge quantities of methanol injection. This decision is more about class rules, weight targets, and setup/fab simplicity in my opinion, but as always, weigh the pros and cons and make the best decision you can for your own particular situation.
​
​
​
​
​
​
​
​
​
​
​
​
​
​
​
​
​
Update:
To show the correlation between methanol boiling point (pressure corrected) and actual IAT, when injecting enough methanol that it should cool below this point, here is a chart of some data between 40 and 60 psi. This is all from runs on my car between 2015-2016. Note that the boiling point increases with pressure. Data was collected at the end of drag passes or dyno runs where IAT had stabilized, and an average taken over 1 second or so to avoid grabbing any odd peaks or offsets in offsets due to sample rate. There is a little noise above 45 psi, 20 degrees or so, but it still averages around the methanol BP pretty well. This data wasn't cherry picked or preselected in any way. As always, this isn't a perfect test done in a lab. It's a race car, and there are variables. But I hope this proves interesting to people.

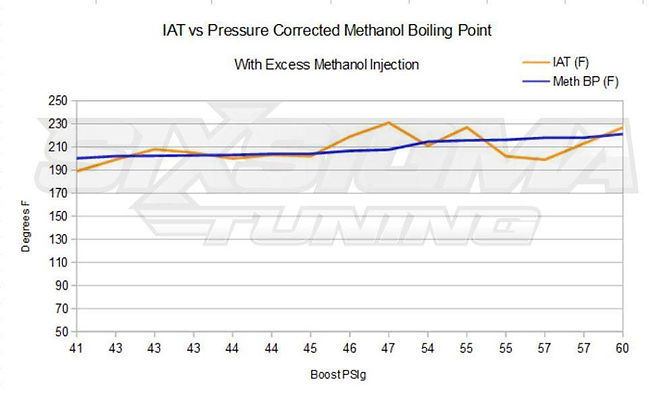